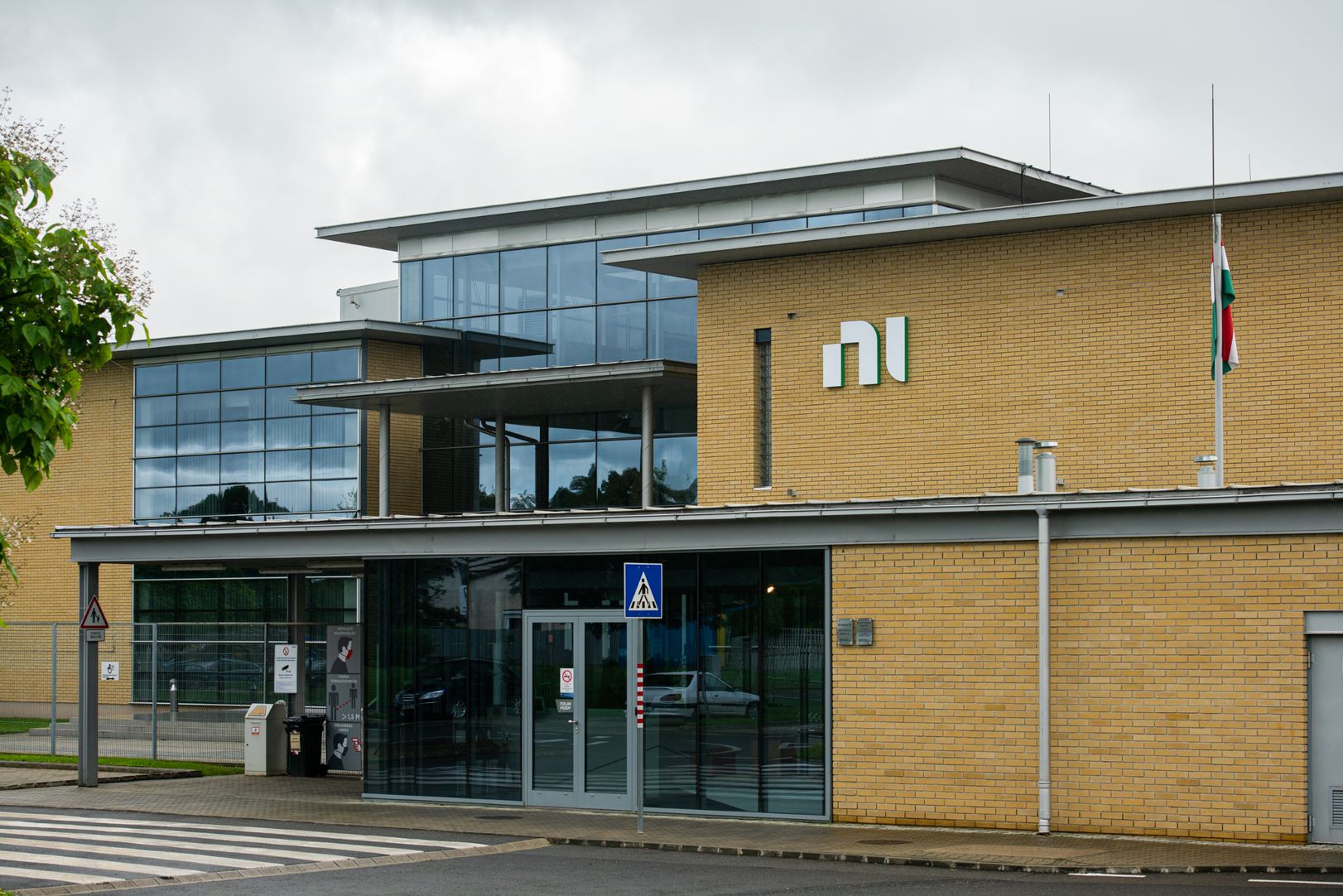
NI Hungary Kft.
Tesztelési és mérési technológiái segítségével, az NI több mint négy évtizede működik együtt a tehetséges mérnökökkel és vállalkozásokkal a világ legsürgetőbb kihívásainak megoldásában. Az NI szoftverhez kapcsolódó megközelítése – az adatoktól és az automatizálástól kezdve a kutatásig és az érvényesítésig – segíti vevőit az új innovációk gyorsabb, megbízhatóbb és biztonságosabb tesztelésében.
A 2001-ben létrehozott debreceni leányvállalatnál a gyártást szakképzett mérnökök támogatják, a kutatás-fejlesztési mérnökcsoport tevékenysége révén pedig a cég igazi tudásközponttá nőtte ki magát a régióban.
Az NI debreceni gyárában végzett gyártási tevékenység tulajdonképpen magas komplexitású, magas fokon automatizált elektronikai összeszerelést jelent, melynek során elektronikus alkatrészekből meghatározott feladatokra tervezett készterméket (szerelvényt) állítanak elő. Az NI, mint globális vállalat rendkívül sokféle terméket gyárt, azonban a termékek jellemzően kis sorozatokban készülnek ami egy ún. „High Mix Low Volume” gyártási struktúrát eredményez. Ez teszi a gyártási folyamatukat egyedivé. A debreceni gyárban készülő, egyedileg azonosított termékféleségek száma több, mint 2000, a sorozatnagyság általánosan 10 és 500 között alakul, de előfordul 1-2 darabos gyártás is.
A felhasznált alkatrészek, illetve alapanyagok szempontjából a gyártási folyamat az alkatrészek érkeztetésével és az Alapanyag Raktárba történő átmeneti betárolásukkal kezdődik, ahol már a későbbi felhasználásuknak – azaz az alkalmazott technológiának – megfelelően rendezve történik az elhelyezésük. (Külön lokációban pl. az automata beültető gépeken felhasznált tekercses alkatrészek, kézi beültetésű alkatrészek, mechanikus alkatrészek, burkolatok, stb.) Szintén az Alapanyag Raktárban kerülneka később alkatrészként felhasznált előzőleg gyártott félkész termékek is.
A termékek gyártási technológiájában az elektronikus alkatrészek beépítésére két főbb szerelési technológiát különböztetnek meg: a felületszerelési technológiát és a furatszerelési technológiát. Ezek a gyártási folyamatban egymást követik. A gyártás a felületszerelési technológiával kezdődik.
A felületszerelési technológia gépei funkciójuknak megfelelően gyártósorokba rendezve biztosítják a megfelelő termék építési folyamatot. Ezen a technológiai lépésen történik a termékek legösszetettebb elektronikus áramköreinek az összeállítása. Egy átlagos termékbe ekkor jellemzően kb. 300-500 db elektronikus alkatrész épül be. A gépek működése döntően automatizált.
A felületszerelési technológia a következő főbb lépésekből áll: első lépésként a forrasz paszta felvitele történik meg a termék alapját képező nyomtatott áramköri lapra (angol rövidítésből PCB-re) stencil nyomtatási eljárással. Majd az alkatrészek felhelyezése következik a felvitt forraszpasztára – ez az ún. beültetési lépés, amit gyártósoronként 2-3 vagy szükség szerint több beültetőgép végez. A beültetőgépek után minden gyártósorban vizuális ellenőrző állomások vannak kialakítva, ahol a termékek szemrevételezéses ellenőrzése történik. Ez is jelzi, hogy a modern és automatikus gépek alkalmazása mellett sem nélkülözhető az emberi munkaerő szakértelme. A következő technológiai lépés a forrasztás, mely során megtörténik az előzőleg beültetett alkatrészek nyomtatott áramköri laphoz való forrasztása egy ún. újraömlesztéses, vagy más néven alagútkemencében. Ehhez a kemence a továbbító sínein áthaladó szerelvényt – úgy mint nyomtatott áramköri lapot, alkatrészeket és forrasztópasztát – teljes tömegében felmelegíti a forrasztó paszta olvadási hőmérséklete fölé ahol az megolvad majd kihűlve létrehozza a forrasztott kötést. A felületszerelési technológia utolsó lépéseként automatizált optikai ellenőrzés történik. Erre a célra úgynevezett AOI gépek vannak telepítve a gyártósorokban, amelyek a panel felosztott területeiről fényképfelvételeket készítenek és azok elemzésével állapítják meg, hogy megfelelő-e a termék minősége.
A felületszerelt alkatrészek beépítése után a furatszerelt alkatrészek beépítése következik. A furatszerelt alkatrészek beültetése döntően kézi szerelési eljárással történik, majd következő lépésként megtörténik ezeknek az alkatrészeknek a forrasztása is. A furatszerelt alkatrészek forrasztása úgynevezett hullámforrasztási vagy szelektív forrasztási technológiával történik. Mindkettő jellemzője, hogy a forrasztás áramoltatott olvadt állapotú forraszanyaggal történik. Ezzel hozzák érintkezésbe a panel alsó oldalát, illetve az ott kinyúló alkatrész lábakat. A panel fémezett falú furataival, illetve az alkatrész lábakkal érintkező forrasztóanyag a kapilláris jelenség hatására kitölti a fémezett falú furat és az alkatrész láb közötti térfogatot majd megszilárdulva létrehozza a forrasztott kötést. A furatszerelt alkatrészek forrasztása után ismét vizuális ellenőrzési lépés következik a termék minőségének az ellenőrzésére.
A felületszerelt és furatszerelt alkatrészek beültetésével minden elektronikus alkatrész beépítése megtörtént. Ezután a gyártási folyamatban a készre szerelés és a tesztelési lépések következnek. A termék a készre szerelés során éri el azt az állapotot, amivel a végfelhasználó találkozik. Ez a lépés terméktől függően egyszerű vagy akár nagyon komplex is lehet.
A termékek a gyártásuk során több tesztelési lépésen is átesnek. Ezek közül talán a legfontosabb az úgynevezett funkcionális teszt, ami minden egyes terméken megtörténik azok készre szerelt állapotában. A funkcionális teszt során a termékek valós – vagy a valósat szimuláló – üzemi körülmények közé kerülnek és megtörténik a megfelelő működésük teljeskörű ellenőrzése.
A termékek végellenőrzés és csomagolás után a Készáru Raktárba kerülnek, ahol úgynevezett kiszállítási egységeket állítanak össze belőlük – ami lehet egy darab termék vagy egy sok tételből álló csomag is – majd innen történik a kiszállítás. Az NI Debrecenből szinte a világ összes pontjára szállít. A legkülönlegesebb megrendelés az elmúlt évekből talán az Északi Sarkról érkezett.
A gyártás számokban:
Egyszerre kb. 20.000 db termék van gyártásban vagy előkészítés alatt.
Minden terméket letesztelnek.
A legkisebb alkatrész, amit beépítenek termékekbe 0,6 x 0,3 mm, kb. mákszem nagyságú.
300+ teszt állomás, közel 100 szerelő/beültető/javító állomás a Termelésben.
5 féle új termék/hét Debrecenben.
Galéria:
A 2001-ben létrehozott debreceni leányvállalatnál a gyártást szakképzett mérnökök támogatják, a kutatás-fejlesztési mérnökcsoport tevékenysége révén pedig a cég igazi tudásközponttá nőtte ki magát a régióban.
Az NI debreceni gyárában végzett gyártási tevékenység tulajdonképpen magas komplexitású, magas fokon automatizált elektronikai összeszerelést jelent, melynek során elektronikus alkatrészekből meghatározott feladatokra tervezett készterméket (szerelvényt) állítanak elő. Az NI, mint globális vállalat rendkívül sokféle terméket gyárt, azonban a termékek jellemzően kis sorozatokban készülnek ami egy ún. „High Mix Low Volume” gyártási struktúrát eredményez. Ez teszi a gyártási folyamatukat egyedivé. A debreceni gyárban készülő, egyedileg azonosított termékféleségek száma több, mint 2000, a sorozatnagyság általánosan 10 és 500 között alakul, de előfordul 1-2 darabos gyártás is.
A felhasznált alkatrészek, illetve alapanyagok szempontjából a gyártási folyamat az alkatrészek érkeztetésével és az Alapanyag Raktárba történő átmeneti betárolásukkal kezdődik, ahol már a későbbi felhasználásuknak – azaz az alkalmazott technológiának – megfelelően rendezve történik az elhelyezésük. (Külön lokációban pl. az automata beültető gépeken felhasznált tekercses alkatrészek, kézi beültetésű alkatrészek, mechanikus alkatrészek, burkolatok, stb.) Szintén az Alapanyag Raktárban kerülneka később alkatrészként felhasznált előzőleg gyártott félkész termékek is.
A termékek gyártási technológiájában az elektronikus alkatrészek beépítésére két főbb szerelési technológiát különböztetnek meg: a felületszerelési technológiát és a furatszerelési technológiát. Ezek a gyártási folyamatban egymást követik. A gyártás a felületszerelési technológiával kezdődik.
A felületszerelési technológia gépei funkciójuknak megfelelően gyártósorokba rendezve biztosítják a megfelelő termék építési folyamatot. Ezen a technológiai lépésen történik a termékek legösszetettebb elektronikus áramköreinek az összeállítása. Egy átlagos termékbe ekkor jellemzően kb. 300-500 db elektronikus alkatrész épül be. A gépek működése döntően automatizált.
A felületszerelési technológia a következő főbb lépésekből áll: első lépésként a forrasz paszta felvitele történik meg a termék alapját képező nyomtatott áramköri lapra (angol rövidítésből PCB-re) stencil nyomtatási eljárással. Majd az alkatrészek felhelyezése következik a felvitt forraszpasztára – ez az ún. beültetési lépés, amit gyártósoronként 2-3 vagy szükség szerint több beültetőgép végez. A beültetőgépek után minden gyártósorban vizuális ellenőrző állomások vannak kialakítva, ahol a termékek szemrevételezéses ellenőrzése történik. Ez is jelzi, hogy a modern és automatikus gépek alkalmazása mellett sem nélkülözhető az emberi munkaerő szakértelme. A következő technológiai lépés a forrasztás, mely során megtörténik az előzőleg beültetett alkatrészek nyomtatott áramköri laphoz való forrasztása egy ún. újraömlesztéses, vagy más néven alagútkemencében. Ehhez a kemence a továbbító sínein áthaladó szerelvényt – úgy mint nyomtatott áramköri lapot, alkatrészeket és forrasztópasztát – teljes tömegében felmelegíti a forrasztó paszta olvadási hőmérséklete fölé ahol az megolvad majd kihűlve létrehozza a forrasztott kötést. A felületszerelési technológia utolsó lépéseként automatizált optikai ellenőrzés történik. Erre a célra úgynevezett AOI gépek vannak telepítve a gyártósorokban, amelyek a panel felosztott területeiről fényképfelvételeket készítenek és azok elemzésével állapítják meg, hogy megfelelő-e a termék minősége.
A felületszerelt alkatrészek beépítése után a furatszerelt alkatrészek beépítése következik. A furatszerelt alkatrészek beültetése döntően kézi szerelési eljárással történik, majd következő lépésként megtörténik ezeknek az alkatrészeknek a forrasztása is. A furatszerelt alkatrészek forrasztása úgynevezett hullámforrasztási vagy szelektív forrasztási technológiával történik. Mindkettő jellemzője, hogy a forrasztás áramoltatott olvadt állapotú forraszanyaggal történik. Ezzel hozzák érintkezésbe a panel alsó oldalát, illetve az ott kinyúló alkatrész lábakat. A panel fémezett falú furataival, illetve az alkatrész lábakkal érintkező forrasztóanyag a kapilláris jelenség hatására kitölti a fémezett falú furat és az alkatrész láb közötti térfogatot majd megszilárdulva létrehozza a forrasztott kötést. A furatszerelt alkatrészek forrasztása után ismét vizuális ellenőrzési lépés következik a termék minőségének az ellenőrzésére.
A felületszerelt és furatszerelt alkatrészek beültetésével minden elektronikus alkatrész beépítése megtörtént. Ezután a gyártási folyamatban a készre szerelés és a tesztelési lépések következnek. A termék a készre szerelés során éri el azt az állapotot, amivel a végfelhasználó találkozik. Ez a lépés terméktől függően egyszerű vagy akár nagyon komplex is lehet.
A termékek a gyártásuk során több tesztelési lépésen is átesnek. Ezek közül talán a legfontosabb az úgynevezett funkcionális teszt, ami minden egyes terméken megtörténik azok készre szerelt állapotában. A funkcionális teszt során a termékek valós – vagy a valósat szimuláló – üzemi körülmények közé kerülnek és megtörténik a megfelelő működésük teljeskörű ellenőrzése.
A termékek végellenőrzés és csomagolás után a Készáru Raktárba kerülnek, ahol úgynevezett kiszállítási egységeket állítanak össze belőlük – ami lehet egy darab termék vagy egy sok tételből álló csomag is – majd innen történik a kiszállítás. Az NI Debrecenből szinte a világ összes pontjára szállít. A legkülönlegesebb megrendelés az elmúlt évekből talán az Északi Sarkról érkezett.
A gyártás számokban:
Egyszerre kb. 20.000 db termék van gyártásban vagy előkészítés alatt.
Minden terméket letesztelnek.
A legkisebb alkatrész, amit beépítenek termékekbe 0,6 x 0,3 mm, kb. mákszem nagyságú.
300+ teszt állomás, közel 100 szerelő/beültető/javító állomás a Termelésben.
5 féle új termék/hét Debrecenben.
Galéria: